Illuminating the Crafting Journey: How Solar Cells are Manufactured
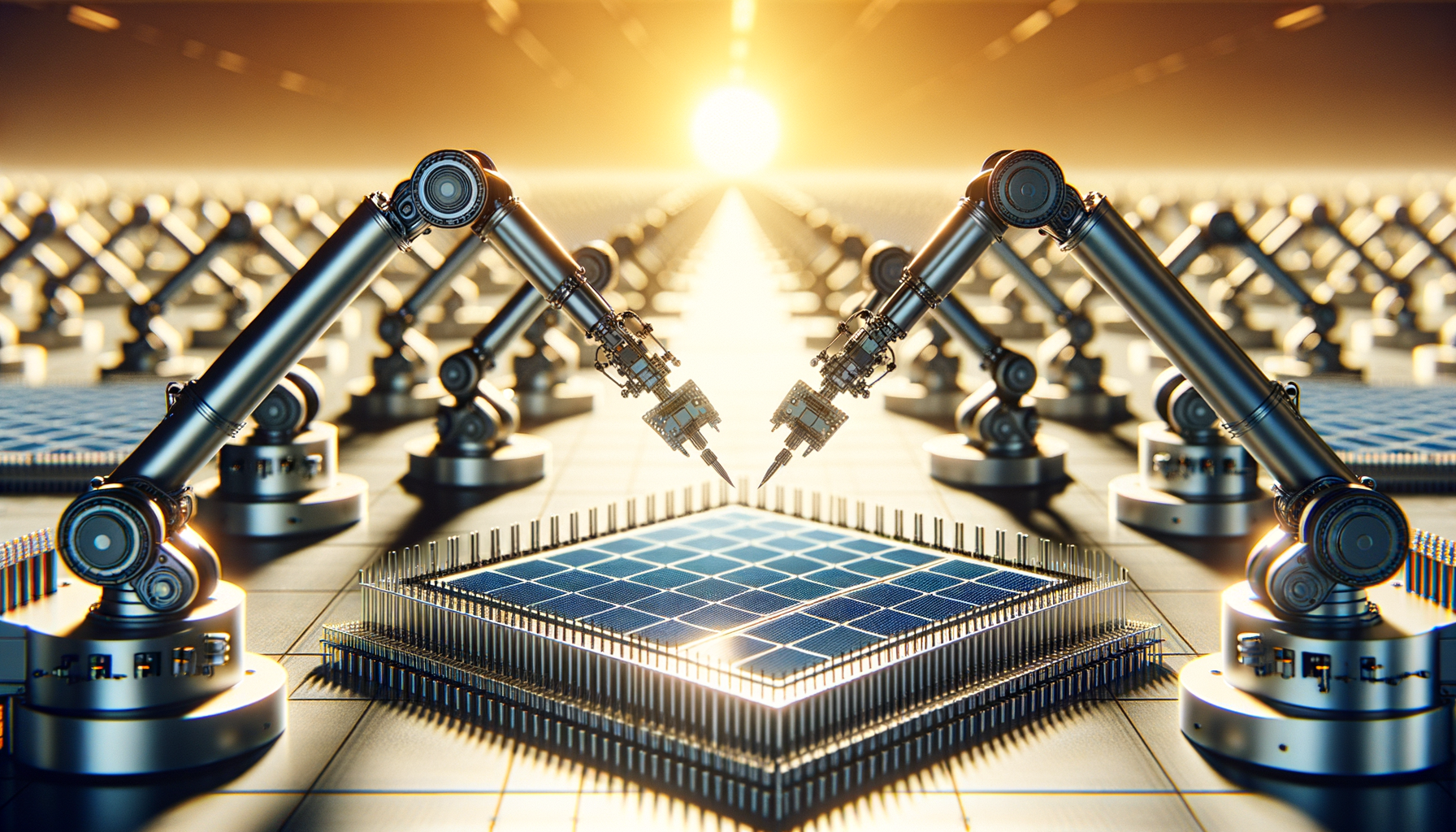
Updated 4 months ago
Illuminating the Crafting Journey: How Solar Cells are Manufactured
Transforming sunlight into electricity is no simple feat. It requires precision, technological sophistication, and a deep understanding of materials science. Solar cells, the building blocks of solar panels, are crafted through an intricately detailed process that turns raw silicon into a power harnessing marvel. This article shines a light on the manufacturing journey of solar cells, revealing each step in creating this sustainable energy technology.
The Birth of a Solar Cell: Silicon's Journey From Sand to Energy
The essential component of any solar cell is silicon, a material derived from the abundant resource of quartz sand. Silicon's metamorphosis is a tale of purification and precision engineering, resulting in the awe-inspiring capacity to capture solar energy.
Polysilicon Production and the Art of Absolute Purity
The first chapter in the story of solar cell manufacturing is the production of polysilicon, a material notorious for its need for high purity. This journey begins with placing silicon dioxide within an electric arc furnace where a carbon arc refines the material by separating the oxygen - a process leaving behind silicon with a mere 1% impurity.
Nevertheless, this level of purity does not suffice for the demands of photovoltaic technology. In pursuit of higher purity, producers often turn to the Siemens process or other innovative methods to obtain the polysilicon rods or beads required for the next phase.
From Silicon to Wafers - The Blueprint of a Solar Cell
Silicon ingots - cylindrical monocrystalline or large-grained multicrystalline structures - emerge from the purified polysilicon. These ingots are then sliced into thin discs or wafers with the precision of diamond-coated wire saws. Like skilled sculptors, machines carve these wafers into the shapes that will later compose the light-capturing surfaces of solar cells.
N-Type and P-Type: Setting the Stage for Electrical Magic
With the silicon wafer ready, it's time for doping - a process of infusing the wafer with specific elements to create n-type and p-type silicon, the fundamental yin and yang of a solar cell. These treated wafers are then coated with an anti-reflective substance, usually involving materials such as titanium dioxide, ensuring maximum sunlight absorption.
The Conductor Orchestra: Screen Printing and Metallization
Silver, known for its superior conductivity, plays a starring role in the next act. Screen printing carefully applies silver pastes on the silicon wafer, creating the conductive busbars and fingers, ultimately responsible for the flow of generated electrical currents.
Assembling Solar Symphony: Cells to Modules
In a crescendo of collaboration, individual solar cells are joined together through tabbing and stringing, aligning their electrical outputs in harmony. They're then laid onto a substrate of glass and encapsulated with EVA (ethylene vinyl acetate) or similar polymers, followed by backing with durable materials and framed with aluminum - a protective embrace preparing them for a lifetime under the sun.
The Performance: Testing for Endurance and Efficiency
Before these solar cells can take the stage and perform, they undergo rigorous testing. Manufacturers examine each panel for its integrity, verifying that it can withstand the vagaries of weather and the passage of time, all while producing electricity at expected efficiency levels.
The Encore: Solar Cells to Society
Once tested, these solar marvels are ready for their global debut, dispatched to rooftops, solar farms, and beyond - each an individual contributing to the choir of clean energy and sustainability.
![close up of solar cells being manufactured // ALT: Precision in solar cells manufacturing // Prompt: A detailed view of a solar cell production line with robotic arms and solar cells illuminated by bright factory lighting, showcase the high-tech manufacturing process, aspect ratio: 4:3]].
The Global Stage: Where Solar Cells Come to Life
Though the story of a solar cell begins with simple sand, their manufacturing stages span across the globe. Production facilities range from the United States to Asia, each offering nuances in quality control and manufacturing practices. For those seeking solar technology crafted closer to home, plenty of options exist to accommodate a preference for American-made ingenuity.
The Final Bow: Innovation Beyond Silicon
Silicon isn't the only contender on the solar stage. Innovations continue to emerge, such as thin-film technologies like cadmium telluride (CdTe) and amorphous silicon - each with its unique manufacturing processes and applications.
A Clear Future: Translucent Solar Innovation
As the curtain falls on our exploration of solar cell manufacturing, we cannot ignore the bright future ahead. Advancements in PV technologies hint at a world where every surface could potentially harness the sun's energy - from windows to vehicle skins.
Embrace Your Solar Potential
Having traversed through the meticulous process of bringing solar cells to life, perhaps you're contemplating how this technology could illuminate your own energy future.
Whether upgrading your home, scaling up a business, or contributing to a greener planet, understanding the journey of these radiant wonders can deepen your appreciation for every sunlit moment they capture. Dive into the potential of solar energy and discover the savings that await under the sun's generous glow.
FAQs about Solar Cell Manufacturing
What makes a high-quality solar panel? Heritage and pride in production ensure the highest caliber panels enter the market. Continuous monitoring and stringent quality assurance during each manufacturing step result in a solar panel that not only meets but exceeds expectations.
Can solar panels withstand harsh weather conditions? Yes. Robust testing against intense weather, heat, and wear establishes solar panels as durable and dependable actors on the energy stage, consistent in their performance rain or shine.
What are the efficiency differences between solar panel types? Monocrystalline panels poised with single-crystal silicon boast the highest efficiency, followed by polycrystalline panels with their multi-crystalline approach. Thin-film panels trade efficiency for flexibility in application, finding their niche in spaces where traditional panels may not perform as well.
Are thin-film solar panels a viable choice for homeowners? Traditionally, thin-film panels have found their forte in large-scale utility projects. However, as technology evolves, so do their applications, making thinner, lighter, and more adaptable panels an exciting prospect for the residential market.
![solar panel testing for quality and weather resistance // ALT: Solar panels enduring quality tests // Prompt: An image of solar panels undergoing stress tests, simulating extreme weather conditions and measuring performance and durability, aspect ratio: 16:9]]
By becoming versed in the nuances of solar cell manufacturing, you're not only informed but empowered to make choices that resonate with your vision for a sustainable and energy-independent future.
As the day turns to dusk and solar cells have a moment's rest, we're reminded of their tireless efforts, their silent production of clean energy, and the human ingenuity that made their existence possible. Embrace the innovation, and let the sun power your next chapter.